Industrial Adhesives: Essential Construction Tools for Manufacturing
- snehacmi01
- Jul 18, 2024
- 3 min read
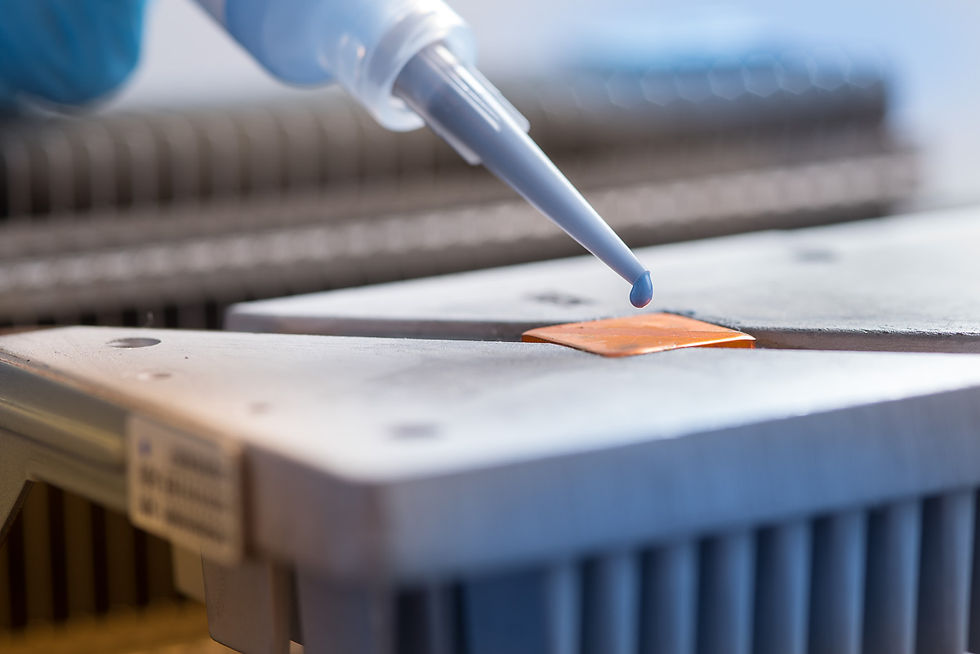
Adhesive Chemical Types
Many types of adhesives are used in industrial manufacturing settings, each with their own strengths and weaknesses depending on the application. Understanding the main adhesive types can help manufacturers choose the right option for their needs.
Cement and Emulsion Adhesives
Cement and emulsion adhesives are water-based, making them easy to clean up. However, they are weaker bonds than other options and may not withstand heavy stress or weather exposure long-term. Cement adhesives dry slowly while emulsion adhesives dry more quickly. Both are economical choices for light-duty indoor applications.
Solvent-Based Adhesives
Solvent adhesives contain organic compounds like acetone or toluene to keep the binder fluid. They are fast-drying and create strong, durable bonds instantly. However, solvents are volatile organic compounds (VOCs) that release air pollutants during drying. Strict regulations apply to their use. Solvent adhesives work well for wood, plastics and rubber but require ventilation.
Reactive Hot Melt Industrial Adhesives
Hot melt adhesives melt to a liquid when heated and harden rapidly on cooling to form strong bonds. Varieties include ethylene-vinyl acetate (EVA), polyurethane and polyolefin. They bond quickly without solvents, are weatherproof and create immediate handling strength. However, melting and application equipment is specialized and they require high application temperatures.
Reactive Adhesives
Epoxy, acrylate and silicone Industrial Adhesives chemically react or cure when mixed with a hardener or catalyst. This allows for exceptional heat and chemical resistance along with durable long-term bonding. They maintain strength over a wide temperature range and in wet or harsh conditions. Specialized application is needed and care must be taken with their reactivity.
Industrial Adhesives Selection Factors
Several factors influence which type of adhesive works best depending on the manufacturing needs:
- Bond Strength - Weight and stress loads determine durability requirements.
- Substrate Type - Different materials like metal, wood or plastic require compatible adhesives.
- Temperature Range - Adhesives withstand different heat and cold conditions.
- Production Speed - Curing times affect process flow and throughput.
- Toxicity - Ventilation and material handling procedures rely on adhesive chemistry.
- Regulations - Restrictions on VOC emissionsrequire compliance verification.
- Cost Effectiveness - Application equipment and lifespan factor into total cost analysis.
Proper Surface Preparation
Regardless of the adhesive, surface preparation is key to creating a durable bonded joint. Manufacturing surfaces must be clean, dry and roughened for adhesion. Steps include:
- Degreasing to remove oils, dirt and other contaminants that could weaken the bond. Solvents or alkaline cleaners may be used.
- Abrasion to break through any oxide layer and create microscopic tooth or texture for adhesive interlocking. Sanding, grinding or chemical etching achieves this.
- Priming can enhance specific material adhesion through chemical bonding between the primer layer and adhesive. This gives the bond better shear and peel strength.
Quality Control Assurance for Industrial Adhesives
Testing bonded assemblies throughout production validates process consistency and ensures structural integrity. Non-destructive methods catch defects early:
- Pull Testing tears bonded samples apart to quantify bond strength in pounds of force withstood.
- Shear Testing applies forces parallel to the bonded plane to simulate in-use stresses.
- Thermal Cycling subjects samples to repeated temperature variations to verify longevity.
- Solvent Resistance soaks assemblies then pulls to check permeability.
- Microscopy examines bondlines for voids or imperfections at the adhesive-substrate interface.
With proper selection and application of industrial adhesives, manufacturers gain a durable, economical joining method suitable for high-volume production. Their adhesion technologies reliably connect materials into assemblies and complete mechanisms. Ongoing QC monitoring further ensures bonded components will perform as designed throughout product lifecycles.
Get more insights on Industrial Adhesives
About Author:
Money Singh is a seasoned content writer with over four years of experience in the market research sector. Her expertise spans various industries, including food and beverages, biotechnology, chemical and materials, defense and aerospace, consumer goods, etc. (https://www.linkedin.com/in/money-singh-590844163)
Comments